Inline heating of liquids or slurries is a requirement in many food, chemical, pharmaceutical and pulp and paper operations. An unlimited and instantaneous supply of hot water is needed in a multitude of industrial applications.
Designers have many choices for heating water, liquids or slurries, but Direct Steam Injection (DSI) Heaters should be at the top of the list of options for these challenging applications.
Why choose DSI?
- DSI offers precise temperature control within ±1° C.
- It is easy to install and can be used wherever medium to high-pressure steam is available.
- Compared to alternatives such as tank steam sparging or indirect heat exchangers, DSI Heaters can cut fuel costs by up to 28%, because 100% of the available energy from the steam is instantly absorbed by the liquid.
- DSI is compact and quiet; the Pick DSI operates at a noise level below 85 dBA, far lower than other systems. Additionally, it features a low pressure drop (less than 2 PSI) and a low differential between steam and water pressures, eliminating damaging vibration and steam hammer.
- DSI has low maintenance costs: Pick Heaters have only one moving part, which can be inspected easily and is relatively inexpensive to replace.
- Finally, DSI is environmentally safe and non-flammable, unlike heat transfer fluids that require special handling and constant monitoring.
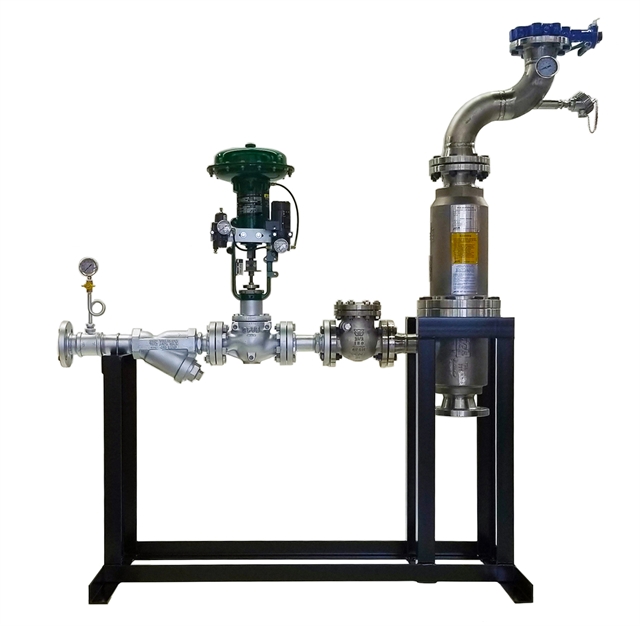
Figure 1: Energy-efficient Direct Steam Injection is used in many industrial processes.
Examples of DSI in Industrial Processes
DSI is superior to indirect exchangers for heating water in industrial applications because it provides a rapid response to changing process conditions and enables precise temperature control within a single degree C.
DSI heating is suitable for many industrial processes. Here are a few examples from different industries.
Many processes in the chemical industry require water temperature to be precisely controlled before adding it to a batch process. A DSI System provides instant temperature control, reducing the cycle time and increasing productivity. DSI is also ideal for dispersing gas into a liquid, mixing two condensate steams or heating a large-capacity, closed-loop jacketed vessels, tanks and blenders, as in this example.
In food processing, hot process water at variable demands is required for applications like plant sanitization, CIP, batch hot water, pasteurizing, bottle, belt, tote and case washing and hose stations where instantaneous and accurately controlled hot water must be available to meet stringent plant demands. Here is an example of a central hot water system for plant hose station service.
The energy and power industry uses DSI in numerous applications, including reverse osmosis (R/O) systems used in the treatment of boiler feed water, and FGD hot slaker water for SO2 emissions reduction. DSI systems are more compact than indirect heat exchangers, giving designers much more design and installation flexibility. Here is an example of a DSI application for a hot water resin bed regeneration system.
In pharmaceutical processing, DSI technology is used in such applications as the continuous-flow treatment of bio-waste. The precise temperature control enables living cells to be killed or inactivated, then cooled before disposal. For example, one waste steam inactivation system required the waste from multiple reactors to be heated to 140° C, held for a period of time, then cooled to 60° C. Read more about waste inactivation here.
Other general industrial examples include parts washers, slurry heating and filter back flushing.
Pick Heaters DSI Product Portfolio
Pick Heaters is a leading manufacturer of DSI Heating Systems. Pick produces DSI Heaters in 10 standard sizes for liquid flow rates up to 5,000 gallons per minute (GPM), and steam flow rates up to 50,000 lb/hr.
Pick's product portfolio includes constant and variable flow water and liquid heaters, sanitary cookers, slurry heaters, condensate mixers, nitrogen injectors, heaters for high pressures and high flow rates and heaters constructed from Hastelloy, Titanium, Inconel, AL-6XN and other special alloys.
Review Pick's comprehensive set of resources including application notes, articles, video and case studies covering a wide range of industrial solutions.
For more information - contact us.