There’s a well-known proverb about necessity being the mother of invention, which is something of a poetic way to say that solving challenges often involves approaching them in new and unique ways — and, once solved, the resulting innovation can be applied to similar challenges. This saying can apply to fulfilling the specific requirements of industrial environments as they present themselves, which often produces lasting solutions with the power to transform everyday industrial practices.
A case in point can be seen in the high-pressure hot water (HPHW) systems commonly used for plant sanitation. Pick Heaters, an American manufacturer of direct steam injection (DSI) heaters, used a unique approach to meet the requirements of a specific customer and in the process hit upon a system design with an unprecedented degree of utility. The system has since been duplicated and adapted for numerous other customers with similar needs.
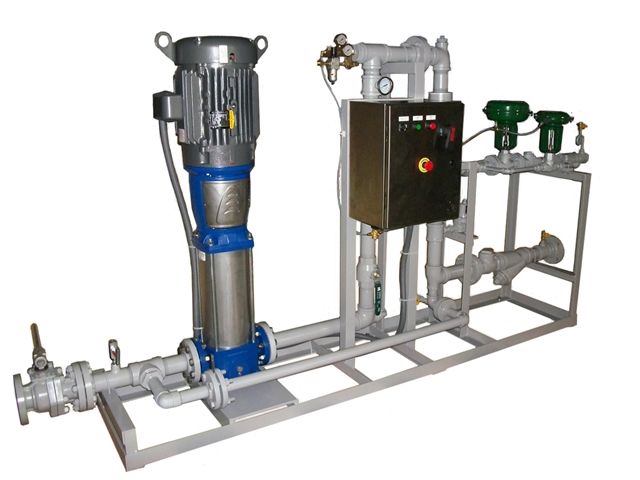
Figure 1. Pick’s approach was to combine two of its primary design strategies into a single system:
a constant-flow DSI heater, along with a variable-frequency drive (VFD) on a downstream boost pump.
Direct Steam Injection
Pick’s approach draws upon its method of direct steam injection heating, a technology it developed and patented. The DSI method injects medium- to high-pressure steam directly into liquid, creating an unlimited supply of hot water for industrial processes. Compared to indirect heating methods employed by shell-and-tube and plate-and-frame systems, DSI significantly increases energy efficiency: 100% of the steam’s energy is instantly absorbed by the liquid, resulting in dramatic energy cost reduction. DSI systems offer quick adaption to load changes, which allows precise temperature control within a 1°C range.
Centralized, variable-flow DSI systems are ideally suited to plant sanitation, which typically have multiple use points with wide variations in demand and frequent stop-start cycling. Sized for peak load demand such as second-shift cleanup, variable-flow DSI systems will also accommodate ongoing low-flow requirements throughout the day. Standard systems handle a 12:1 water flow turndown, and dual-control-valve systems can handle water flow turndown requirements as high as 100:1 — all the while providing precise control of outlet temperature.
Combining strategies
Pick was approached by a poultry plant with the dual requirement of heating water and boosting pressure. Enter the need for invention. Pick combined two of its primary design strategies into a single system: a constant-flow DSI heater, along with a downstream centrifugal boost pump. All steam is smoothly condensed within the Pick heater body, with no straight-run downstream piping requirements, allowing the pump to be safely installed after the heater discharge. With this approach both temperature and pressure can be controlled at customer’s set point.
As seen in the diagram (Figure 2), the system utilizes independent pressure and temperature control loops. Pump discharge pressure is transmitted to a process controller. This sends a signal to the pump’s VFD to automatically adjust pump speed and maintain the required pressure at any flow rate. In a similar manner, heater outlet temperature is continuously monitored by an RTD and used to regulate steam input to maintain desired hot water temperature. Pick also employed dual steam conditioning valves (SCVs) to regulate steam flow to the heater, satisfying the temperature set point and providing steam flow across the wide water flow turndown range required.
A unique feature of this system is the pump bypass loop. A portion of the water is returned from the pump discharge to the heater inlet through a bypass line with orifice plate. This maintains liquid velocity above a critical level to ensure mixing action inside the heater and rapid feedback of process temperature. This mimics the response of Pick’s variable flow system – providing stable control valve response and accurate temperature control despite frequent and uncontrolled changes in water demand at the use points.
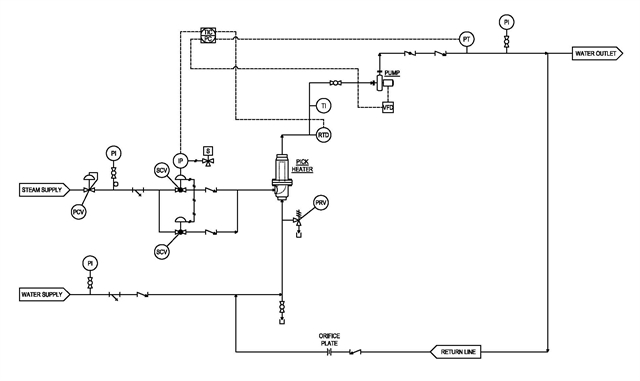
Figure 2. This innovative system design features two control loops: one for pressure and another for temperature.
Innovation equals utility
The result of Pick’s innovative approach is a system with precise automatic control of water supply pressure that can also handle a wide range of water flow rates. As designed, the system accommodates water flow as high as 250 GPM, with downstream use points as low as 7 GPM without system upsets. Preheated water up to 155° F at a pressure of 50 to 60 PSIG can be boosted to 275 PSIG for distribution to up to 15 hose stations throughout the facility.
In addition, of course, the system also offers advantages typical of DSI systems, including instantaneous hot water on demand, precise temperature control and energy efficiency.
Pick’s expertise in DSI system design fulfilled its customer’s requirements while also inventing an approach combining the best of both worlds. Three identical systems have been installed at the same customer facility, and the design has also been adapted for other customers. It is currently available as a pre-engineered, skid-mounted package, with variable sizing to accommodate customer needs.
To learn more about the system — and about Pick’s approach to solving challenges, contact us.