The challenges of heating fluids and providing a steady hot water supply are important to a wide range of industry types, and there are many solutions that engineers employ to meet those challenges. Not all solutions are equal, however; following a selection path designed to save up-front costs may not always be the best strategy. There are numerous factors to consider, including ones that may be less obvious.
Industrial heating solutions typically revolve around indirect heat exchangers, which follow a basic principle of thermodynamics: hotter fluid will transfer its energy to a cooler fluid as it flows through it. The most common type of indirect heat exchange is performed with a shell-and-tube heat exchanger, which uses a bundle of tubes housed within a cylindrical outer shell. One of the fluids flows through the long surface area of the tubes, making thermal contact with the fluid passing through the shell. Heat is thus transferred without the mixing of fluids.
An alternate to the shell-and-tube design is the gasketed plate heat exchanger (GPHE), also known as plate-and-frame, which consists of multiple plates held together with a watertight seal. Holes at the tops and bottoms of the plates serve as fluid inlets and outlets, while the gasket design creates a flow pattern that puts hotter plate surfaces into thermal contact with cooler plate surfaces. Again, heat is transferred indirectly, without the need for fluid mixing. One advantage of a plate-and-frame design over shell-and-tube is that it can be more compact, as offers more thermal contact over a smaller surface area.
There are limits to both types of indirect heat exchangers, however, especially when they are used for applications involving high-temperature fluids or high-pressure steam.
The gaskets in a plate-and-frame unit, for instance, wear quickly when used for high-pressure steam applications; this can create pinhole leaks, which are a safety concern. There is also a significant window of time required for maintenance on a plate-and-frame unit, due to the large number of plates involved.
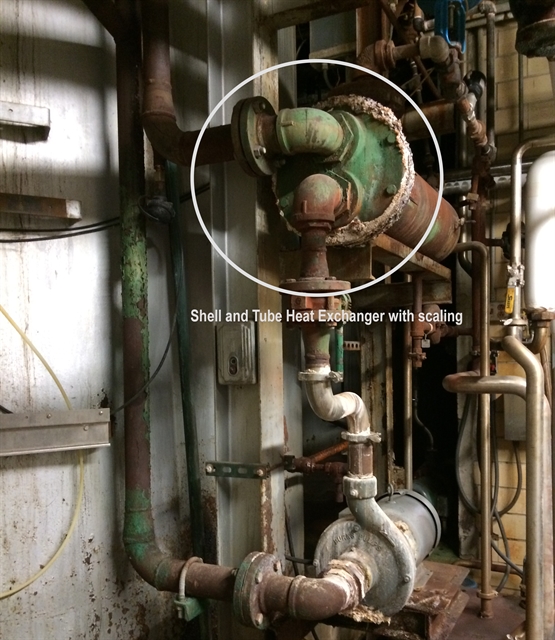
Figure 1. Limescale buildup can be a significant problem for indirect heat exchangers, such as this shell-and-tube unit.
For shell-and-tube units, “hard” water can create a major problem. This phenomenon, caused primarily by calcium and magnesium deposits, is common in the United States and in other parts of the world. As the water is heated, those deposits are liberated to form what is known as limescale. This can build up in the tubes, impacting efficiency, and eventually requiring painstaking maintenance such as acid soaking or drill bit routing. Plate-and-frame units require similar attention, as scaling buildup will diminish plate heat transfer capacity.
In addition, indirect heating methods are inherently inaccurate, requiring ongoing adjustment to maintain set temperatures as flow rate changes. In some applications, such as wash-down hose stations, precise control of temperature is critical; portions of food processing plants, for instance, can be shut down by a visiting inspector if temperature is insufficient for plant sanitation. On the other hand, if water at the hose station is too hot, it can impact both safety and energy costs — the energy expended to reach higher-than-necessary temperatures is simply wasted. This applies to the temperature of process water used across all industries, as well.
Depending upon the application, the initial cost savings offered by indirect heat exchange designs may be more than offset by limiting factors that will become more obvious over time. Fortunately, there is a solution, which is examined in Part 2.
For more information - contact us.